
86 17344894490
service@chalcoaluminum.com
- Алюминиевые ковки для железнодорожных транспортных средств
- Лист алюминиевой пластины для железнодорожных железнодорожных транспортных средств
- Алюминиевый профиль для железнодорожных транспортных средств
Конструкционные детали экструдированного алюминиевого профиля в автомобилестроении
Согласно информации, около 60% существующих заказов европейских производителей локомотивов и транспортных средств составляют транспортные средства с алюминиевым кузовом. 20 лет назад таких заказов было всего 2% – 3%. В настоящее время алюминиевая конструкция применяется в ледовых, tgv-2n, etr460, etr500, поезде Talgo Hotel и других высокоскоростных поездах, а также во многих пригородных и городских железнодорожных транспортных средствах.
Внедрение конструкционных деталей экструдированного алюминиевого профиля началось в начале 1970-х годов. В то время научно-технический прогресс в применении алюминиевых профилей позволил изготовить алюминиевые компоненты по требуемой форме и размерам. Этот алюминиевый компонент был применен к наклонному кузову вагона подходящих поездов в Великобритании. Однако в то время применение экструдированных алюминиевых компонентов не давало большой пользы, то есть более высокие цены на материалы не компенсировались снижением производственной нагрузки. В то время использование крупногабаритных конструкционных деталей только снизило производственную нагрузку на кузов автомобиля на 40% и снизило мертвый вес кузова автомобиля длиной 26 м до 7,5 т, в то время как мертвый вес 26-метрового стального кузова автомобиля составлял 11Т. В 1970-х годах железнодорожный департамент уделял больше внимания расчету общей стоимости всего срока службы транспортных средств (стоимость покупки плюс стоимость эксплуатации и технического обслуживания). Они поняли, что потребление тяговой энергии поездов должно поддерживаться на прежнем уровне, который во многом зависит от собственного веса подвижного состава.
Позднее некоторые новые технические и технологические мероприятия, важнейшие из которых были достигнуты в середине 1980-х годов, такие как принятие метода экструзии крупногабаритных конструкционных деталей двухслойной оболочки, что свело потребность в поперечных креплениях к минимуму, еще больше сократило сроки производства алюминиевого кузова автомобиля, сократив на 50% по сравнению со стальными транспортными средствами, и удалось изготовить двухслойный корпус цилиндра по обычному методу, а затем при вскрытии оконных отверстий все сварочные операции завершаются в процессе унифицированных технических операций, лишь частично с использованием роботизированных технологий и оборудования.
Сейчас, когда железнодорожные ведомства постепенно и все больше сокращают свое участие в разработке новых транспортных средств и реализуют закупочную политику с целью снижения первоначальных производственных затрат и будущих эксплуатационных расходов, производители имеют большую свободу в принятии новых конструкций и материалов для удовлетворения технических требований абонентов и адаптации к тенденциям развития рынка. Конструкционные детали экструдированного алюминиевого профиля также имеют другие преимущества в удовлетворении некоторых строгих требований к конструкции транспортного средства. Например, жесткость двухслойной конструкции экструзии оболочки может гарантировать, что аэродинамический удар, производимый при встрече высокоскоростного поезда, имеет особую ударную вязкость. Еще одной важной особенностью кузова автомобиля с такой конструкцией является его большая продольная жесткость. Соотношение продольной и поперечной жесткости может достигать 70:30, в то время как соотношение стального кузова автомобиля составляет 40:60. Кроме того, алюминиевые профили также могут отвечать требованиям хорошей внешней формы, без использования наполнителей и большого количества ручной работы. Например, для некоторых моделей Немецких федеральных железных дорог, так как не используется наполнитель, после расчета вместе с лакокрасочным покрытием собственный вес может составлять 500кг.
Использование конструкционных деталей экструдированного алюминиевого профиля также ставит производителей автомобилей перед сложными задачами. Они должны найти баланс между ценами на рабочую силу и материалы и заставить дизайнеров стремиться к достижению этого баланса. Следует уточнить, что материал является лишь одним из факторов во всей концепции. Принятый производственный процесс и технический процесс также должны быть детально сформулированы, чтобы он соответствовал производственным мощностям предприятия и балансировал с инвестициями.
Например, для большинства машиностроительных компаний минимизация запасов средств производства является главным приоритетом. Выбор материалов и процессов дизайнерами оказывает на это существенное влияние. ABB имеет производственную линию, которая может выпускать 8 автомобилей с алюминиевым кузовом каждую неделю, что снижает общую стоимость хранения материала на 8%. Однако этот баланс легко разрушается из-за изменений в техническом процессе, вызванных использованием материалов. Например, при переходе от сварки к склеиванию требуется больше суточных резервов, чтобы компенсировать значительное время, необходимое для склеивания упрочнения.
Другим ведущим поставщиком алюминиевых профилей для производства подвижного состава является немецкая компания по борьбе с оборотом оружия. Руководители компании предвидят, что существует большая тенденция развития в стандартизации конструкции транспортных средств и принятии метода модульного проектирования (эта тенденция была усилена за счет рыночного спроса, поэтому она имеет поддержку производителей), и считают, что, учитывая рыночный спрос на регионализацию местных железнодорожных перевозок в Германии, некоторые частные компании будут уделять больше внимания использованию стандартизированной модульной структуры для удовлетворения требований индивидуальных заказчиков в большей степени. В настоящее время различные европейские производители локомотивов и транспортных средств имеют большое количество дизайнерских идей, и эти идеи основаны на дизайне модулей. Эта трансформация в стандартизацию и модульность выгодна как производителям, так и пользователям. Расширение использования алюминиевых профилей в автомобилестроении значительно сократит производственный цикл за счет более широкого использования автоматической сварки.
Также очевидно, что сварные алюминиевые кузова транспортных средств обладают высокой ударопрочностью, что способствует повышению безопасности вождения. АББ инвестировала 1 миллион фунтов стерлингов в организацию и проведение испытаний на разрушение алюминиевой конструкции и получила удовлетворительные и, что более важно, ожидаемые результаты испытаний. Компания также накопила ценный практический опыт в ремонте методов неисправности аварийных транспортных средств. В начале 1994 года испытание на повреждение двухэтажного пассажирского вагона испытательного образца поезда TGV-2n, заказанное GEC Alstom во Франции, доказало, что при силе удара 250 т, из-за поглощенной энергии удара 8 мДж, конструкция экструдировалась в общей сложности на 80 см, а алюминиевый корпус оставался нетронутым в целом.
В то же время признание достоинств алюминиевого кузова автомобиля не лишено проблем. Производители стальных локомотивов и транспортных средств выразили обеспокоенность по поводу акцента на алюминий в процессе производства ледовых поездов в Германии и провели исследование, чтобы подтвердить превосходство стали в 1994 году. Однако, как и прежде, использование стальной конструкции приводит к увеличению примерно на 20% мертвой массы кузова автомобиля.
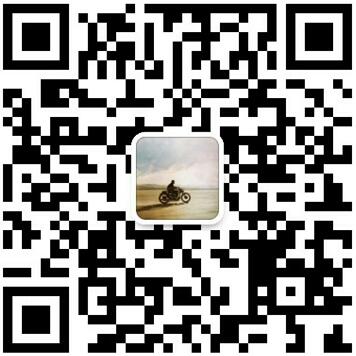
Бесплатное предложение продуктов, добро пожаловать на консультацию в любое время, мы дадим первый ответ. Наша электронная почта: