
86 17344894490
service@chalcoaluminum.com
- Алюминиевые ковки для железнодорожных транспортных средств
- Лист алюминиевой пластины для железнодорожных железнодорожных транспортных средств
- Алюминиевый профиль для железнодорожных транспортных средств
Алюминиевая сотовая панель для рельсовых транспортных средств
Индустрия производства городских железнодорожных транспортных средств имеет жесткую конкуренцию. Энергосбережение и сокращение выбросов – будущее направление развития отрасли. Легкий дизайн – неизбежная тенденция. Применение высокопрочных и низкоплотных материалов всегда было горячей точкой для проектирования транспортных средств и исследований производства. Среди них алюминиевый композитный материал является относительно новым типом материала для производства кузова автомобиля, а его сэндвич-структура выполнена из алюминиевых панелей, основных материалов и алюминиевых панелей, которые обжаты структурными клеями.
Алюминиевая сотовая панель для рельсовых транспортных средств
Алюминиевая сотовая панель для рельсовых транспортных средств производства Chalco Aluminum, после того, как верхняя часть крышки принимает пластину из алюминиевого композитного материала, вес уменьшается с 1095 кг до 965 кг, скорость снижения веса достигает 12%, а эффект снижения веса очевиден. Однако из-за относительно сложной структуры и большой площади поверхности алюминиевого листа обычная сварка MIG не может быть реализована, а сборка и герметизация кузова автомобиля, как правило, завершаются лазерной сваркой или клепкой.
Алюминиевые сотовые панели представляют собой «сэндвичевые» конструкции, состоящие из верхней обшивки, нижней обшивки, сердцевины и кромкооблицовочных профилей, образованных вакуумным термокомпрессивным склеиванием. Среди них, в соответствии с различными положениями различных частей кузова автомобиля, окружающие кромкочные уплотнительные профили могут быть отрегулированы соответствующим образом, а материал среднего сердечника также может быть спроектирован с различной толщиной. Конструкция кузова автомобиля из алюминиевого сплава с использованием пластин из алюминиевого композитного материала, как правило, представляет собой раму, состоящую из алюминиевых профилей кузова автомобиля, гибочных частей и т. Д., А затем клепаную или лазерную сварку пластиной из алюминиевого композитного материала, на которую был установлен композитный материал для формирования кузова автомобиля. Среди них структура пластины из алюминиевого композитного материала в большой части кровли показана на рисунке 1. Было проверено, что только верхняя крышка изготовлена из алюминиевого композитного материала, а вес верхней крышки уменьшен с 1095 кг до 965 кг, а снижение веса верхней крышки достигает 12%, а эффект снижения веса очень очевиден.
Применение алюминиевой сотовой панели может эффективно снизить вес кузова городских рельсовых транспортных средств и обеспечить новый выбор для алюминиевых сплавов корпуса легких материалов. Процесс сварки-клепки-склеивания сочетает в себе изготовление кузова автомобиля, что выдвигает повышенные требования к точности сборки рамы и контролю деформации сварки.
Операции по окраске, такие как пескоструйная обработка, грунтовка и финишное покрытие кузова автомобиля из алюминиевого сплава, должны быть завершены до установки плиты из алюминиевого композитного материала. Чрезмерная температура может легко привести к старению самого алюминиевого композитного материала доски, герметика и т.д., или даже к выходу из строя, сокращая срок службы кузова автомобиля и т.д.
Герметик между алюминиевой композитной пластиной и рамой может эффективно обеспечить водонепроницаемость клепаного соединения. Принимая во внимание такие факторы, как срок службы кузова автомобиля, импортный каучук может быть предпочтительным.
Процесс клепки может соответствовать производственным требованиям кузова автомобиля из алюминиевого сплава из алюминиевого композитного материала пластины. Для мелкосерийного производства может использоваться ручное управление, например, крупные проекты, автоматические линии бурения и клепки могут эффективно снизить интенсивность работы, повысить эффективность производства и обеспечить качество продукции.
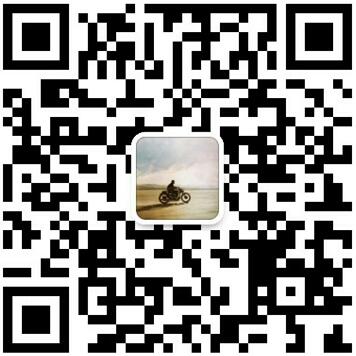
Бесплатное предложение продуктов, добро пожаловать на консультацию в любое время, мы дадим первый ответ. Наша электронная почта: